How digital twins are redefining construction site safety and compliance?
by
Metam technologies
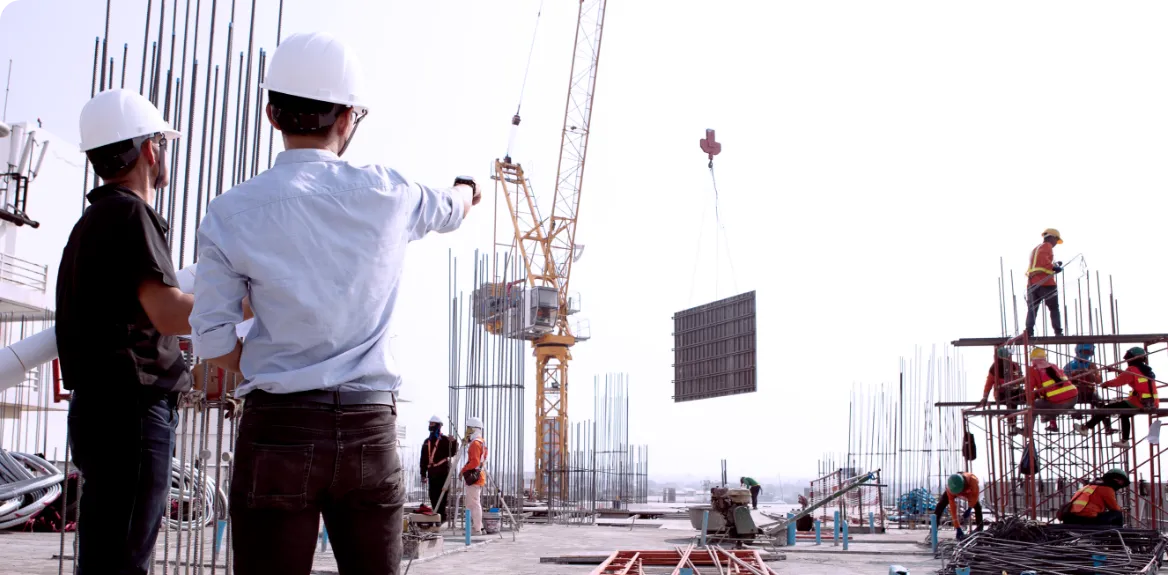
Abstract
Digital twins are reshaping construction site safety and compliance by enabling real-time monitoring, predictive analytics, and automated reporting. This technology helps identify risks early, enhance worker safety, and streamline regulatory adherence. Discover how digital twins are shaping the future of construction.
Table of Content
What are digital twins and how do they apply to construction?

How do digital twins enhance construction site safety?

In what ways do digital twins improve compliance in construction?

What are the challenges of implementing digital twins in construction?

What are the future trends of digital twins in enhancing construction safety and compliance?

Key takeaways

The construction industry faces rising safety risks and strict regulatory compliance demands. Emerging technologies, particularly digital twins, are addressing these challenges by enhancing real-time monitoring and predictive analytics. As construction professionals work to prevent accidents, meet compliance requirements, and manage risks proactively, traditional methods often fall short. Digital twins offer a transformative construction solution by providing dynamic, real-time insights into site conditions, helping to detect hazards early, prevent accidents, and streamline compliance.
According to recent reports, 52% of construction leaders experimented with digital twins in 2024, expecting widespread adoption in 2025. This article explores the role of digital twins in improving construction site safety and compliance, offering in-depth industry insights, real-world applications, and a look at emerging trends that will shape the future.
What are digital twins and how do they apply to construction?
Digital twins are reshaping how construction professionals manage projects by providing real-time data insights into physical assets. These technologies, rooted in manufacturing, are now transforming construction site operations, from monitoring site conditions to enhancing compliance.
Definition of construction digital twins
Digital twins are real-time digital replicas of physical construction assets, created using a combination of sensors, IoT technology, and BIM (Building Information Modeling). Initially developed in manufacturing to simulate product conditions, the technology has made its way into the construction industry, offering more dynamic, data-driven project management capabilities. By constantly updating based on live site data, digital twins allow managers to make informed decisions, address issues proactively, and enhance safety protocols.
This innovation improves efficiency, reduces costs, and supports sustainability efforts in modern construction. As adoption grows, digital twins are becoming a key component of smart infrastructure and predictive maintenance strategies.
Key differences between digital twins and traditional modeling tools
These key differences highlight the advantages of digital twins over traditional modeling tools, providing a more dynamic, data-driven approach to construction site management and safety.
- Real-time updates: Unlike static BIM models, which remain unchanged after construction begins, digital twins continuously evolve with real-time data from the construction site. This ensures that the model reflects the current state of the project at any given time.
- Proactive management: Digital twins offer actionable insights based on live data, enabling construction professionals to predict potential risks and address them before they escalate. Traditional BIM models, on the other hand, are primarily used for design and visualization, with limited real-time updates or predictive capabilities.
- Dynamic monitoring: While BIM provides a detailed design blueprint, it lacks the ability to monitor ongoing changes, such as site conditions, structural performance, and safety hazards. Digital twins allow for continuous monitoring, making them a valuable tool for ongoing project management and decision-making.
- Risk prediction and accident prevention: Digital twins utilize sensors and AI to identify emerging risks (e.g., structural defects, worker fatigue, environmental hazards), allowing for early intervention. Traditional BIM models do not have this proactive feature, making them less effective in preventing accidents during construction.
- Comprehensive integration with IoT: Digital twins are integrated with IoT devices on the construction site, which feed real-time data into the model. This integration provides a more holistic view of site conditions, whereas BIM models typically do not interact with real-time data streams, limiting their scope.
- Enhanced collaboration: With digital twins, all stakeholders, including project managers, contractors, and safety officers, can access up-to-date, actionable information. BIM models, while useful for design collaboration, do not offer the same level of ongoing interaction and real-time updates across all project teams.
How do digital twins enhance construction site safety?
The construction industry is inherently dangerous, with high rates of accidents, injuries, and fatalities. Digital twins offer innovative ways to improve site safety by enabling real-time monitoring, predictive analytics, and scenario-based training.
- Real-time monitoring and hazard detection: By leveraging IoT sensors, digital twins provide continuous monitoring of on-site conditions. Construction managers can detect safety hazards as they emerge, from structural issues like cracks in walls to environmental risks such as hazardous gas emissions or temperature extremes. Immediate alerts allow for quick response, minimizing risk before issues escalate.
- Predictive analytics for accident prevention: Digital twins enable predictive analytics by analyzing historical safety data and real-time information. By identifying patterns, these tools can forecast potential risks, such as high winds, equipment malfunctions, or worker fatigue. This predictive capability helps construction teams take proactive steps to prevent accidents, such as adjusting workflows or reinforcing structures in anticipation of adverse conditions.
- Training and simulation for safety preparedness: Virtual simulations powered by digital twins allow workers to practice responding to potential hazards in a safe, controlled environment. These training modules replicate real-world scenarios, such as fires or structural collapses, allowing workers to improve their response time and safety protocols without the risk of actual harm. This hands-on training enhances preparedness and reduces the likelihood of accidents on-site.
- Worker fatigue monitoring and prevention: A critical yet often overlooked safety risk is worker fatigue. Digital twins can monitor biometric data such as heart rate and body temperature, combined with work schedules, to assess fatigue levels. By identifying when a worker is nearing exhaustion, the system can automatically adjust schedules or trigger alerts to prevent accidents due to fatigue-related errors.
- Automated emergency response planning: Digital twins can also simulate emergency situations, from accidents to natural disasters, helping construction sites develop more efficient emergency response strategies. By running these simulations, construction teams can identify gaps in their response plans, optimize evacuation routes, and ensure that resources are allocated effectively during a crisis.
- Environmental hazard assessment and mitigation: Digital twins also assess environmental conditions on the construction site, such as air quality, temperature, and humidity. These tools provide continuous monitoring, ensuring that the work environment remains safe for construction teams. By identifying hazardous environmental factors early, digital twins enable rapid mitigation efforts, protecting workers from exposure to dangerous conditions like toxic fumes or extreme heat.
In what ways do digital twins improve compliance in construction?
Compliance with safety regulations is a top priority in construction, and digital twins are transforming how compliance is managed. From automating documentation to providing real-time updates on regulatory changes, these tools streamline the compliance process.
Automated documentation and reporting
Digital twins automate the process of documenting safety measures, inspections, and compliance checks. Instead of relying on paper-based logs or manual entry, construction teams can generate real-time, timestamped records that ensure accuracy. This automation reduces the risk of human error, minimizes paperwork, and ensures compliance with safety regulations.
Ensuring adherence to regulations
Digital twins are powered by AI that can track and monitor regulatory changes in real time. Whether it's new OSHA regulations, local building codes, or industry standards, the system keeps construction teams up to date with the latest compliance requirements. This proactive approach ensures that all site processes remain compliant, reducing the risk of fines or delays.
Tracking changes in safety standards and compliance laws
Safety standards and regulations are constantly evolving. Digital twins continuously update with new industry safety guidelines, helping companies stay ahead of the curve. These tools provide automatic notifications when a new regulation is implemented, allowing construction firms to update their practices immediately to maintain compliance.
Data-driven audits and inspections
Conducting audits and inspections is an essential part of maintaining construction site compliance. Digital twins streamline this process by providing accurate, real-time data on site conditions. These digital records simplify inspections, ensuring that auditors have access to up-to-date and verifiable information, making it easier to pass compliance checks.
Using AI for proactive compliance issue identification
AI-powered digital twins not only monitor compliance but also analyze site conditions to flag potential violations before they become major issues. For example, the system may identify areas of non-compliance with fire safety regulations or deviations from approved building plans. This proactive approach helps construction teams address issues before they become costly legal problems.
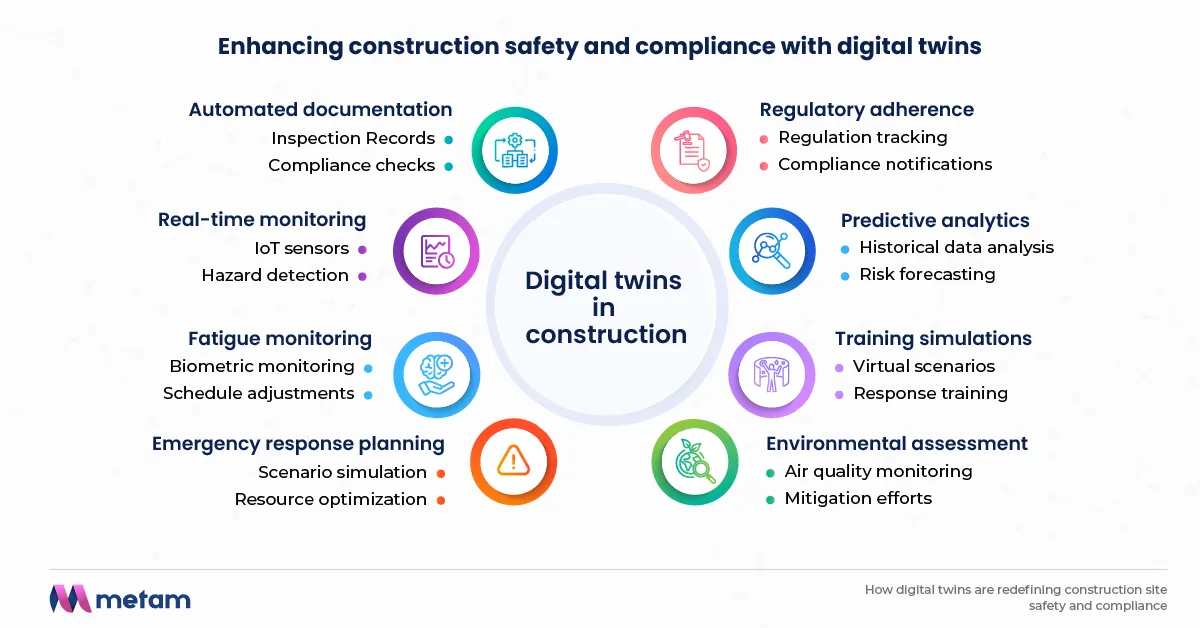
What are the challenges of implementing digital twins in construction?
While digital twins offer numerous benefits, their implementation in construction comes with challenges. From data security concerns to high costs and integration issues, construction firms need to carefully navigate these obstacles to successfully adopt the technology.
- Data security and privacy concerns: The digital twin system collects vast amounts of sensitive data, from construction site conditions to worker information. This makes it an attractive target for cyber threats. Strong encryption and cybersecurity measures are essential to protect data integrity and prevent unauthorized access.
- Integration with existing systems: Many construction firms are already using project management tools and software that may not be compatible with digital twins. Integrating these systems can be complex, requiring customized solutions and potentially significant investments in software upgrades and workforce training.
- Cost and resource considerations: Implementing digital twins requires a significant upfront investment in hardware, software, and specialized training. While the long-term benefits, such as improved safety, efficiency, and compliance, are clear, firms need to weigh these costs against their budget and long-term goals.
- Lack of industry-wide standards for digital twin implementation: Unlike BIM, which has well-established standards, digital twins lack industry-wide protocols for implementation. This fragmentation means that different firms may adopt the technology in varying ways, creating challenges in interoperability and consistency.
- Resistance to technological change within construction firms: Technological adoption in construction is often slow due to cultural resistance, especially when workers are unfamiliar with new tools. Overcoming this resistance requires strategic planning, including training programs and clear communication about the benefits of digital twins.
What are the future trends of digital twins in enhancing construction safety and compliance?
Looking ahead, digital twins are poised to evolve alongside advancements in AI, IoT, and 5G technology, further enhancing safety, compliance, and efficiency across construction sites.
- Integration with artificial intelligence and machine learning: AI will increasingly drive the capabilities of digital twins, allowing for more advanced predictive analytics, automated risk assessments, and compliance tracking. These tools will not only detect problems but will also make decisions and offer actionable solutions.
- Advancements in IoT and sensor technology: IoT sensor technology will continue to improve, providing more accurate and real-time data. This will enhance the ability of digital twins to monitor construction site conditions, enabling faster and more effective responses to emerging hazards.
- Increased industry adoption: As the costs of digital twin technologies decrease and their value becomes clearer, adoption across the construction industry will increase. More companies will implement these tools to improve safety, compliance, and overall project outcomes.
- Blockchain for secure data management in digital twins: Blockchain integration will provide tamper-proof records, improving transparency and security in safety audits and compliance checks. This technology will ensure that digital twin data cannot be altered, offering a new level of trust in the system.
- 5G-enabled digital twins for real-time remote site monitoring: The rollout of 5G networks will allow digital twins to transmit and process data in real time, enabling more effective remote monitoring of construction sites. This will allow construction managers to oversee projects from anywhere, ensuring ongoing safety and compliance.
Key takeaways
Digital twins are revolutionizing construction site safety and compliance by offering real-time monitoring, predictive analytics, and automated planning. These tools help construction firms proactively manage risks, improve worker safety, and maintain compliance with evolving regulations.
However, challenges such as data security, integration with legacy systems, and resistance to change must be addressed for successful implementation. Moving forward, advancements in AI, IoT, 5G, and blockchain will enhance the capabilities of digital twins, positioning them as an industry standard for safety and compliance.
Construction compliance...
This article explores the transformative role of compliance automation in construction health and safety management,...